Got Budget?
As everyone knows, we must have money in the budget or nothing happens. Without it, we cannot add staff to help overworked employees. We cannot buy equipment and supplies nor can we add space to our facilities. Exhibitions become more difficult to complete which certainly makes life more difficult for overworked employees. Worst of all - institutions are having to lay-off those already overworked employees. There is a boatload of sales people hitting the streets harder than ever before trying to get a share of your ever-decreasing budget.
How are we to deal with this “budget problem”? Well, usually the first thing you would think to do is cut costs. But cutting costs can come at a price when service suffers and value you receive for your investment decreases. What you are really looking for is the optimal fit between service and price. When part of your job is to arrange transportation for exhibitions, there are a number of ways you can optimize the value you receive for your investment.
Here are some things to consider that could help your budget:
• Does the entire shipment need climate control service, or can the “non-object” items travel in a less expensive environment?
• Paying for dual driver service can be very expensive. Does the exhibition schedule allow for the objects to travel with dual drivers and the “non-object” pieces to arrive at a slightly later date?
• Can you deck any part of the exhibition? Decking is a service where you create a second floor above the lower level of items on a van. This is accomplished with bars that are attached to the wall of the trailer. This allows use of the space above the floor-loaded pieces without stacking directly on an object or object crate. This does sometimes require a forklift to load and unload. If a forklift is not available at origin and destination then this might not be a viable option, but some items are small and light enough to be decked by hand and decking could then be an option.
• When you have a gap in the schedule and the last venue before the break is many miles away, consider storage at a local fine art facility. Most major markets have established fine art service companies that can provide exhibition quality storage. This will sometimes save the cost of bringing the exhibition back across country to be stored at your facility.
• Consider using non-climate controlled storage for the non-artifact portion of the exhibition. Quite often the cost savings of using non-climate controlled storage outweighs the cost of an extra delivery and pickup for using a second facility. Sometimes the climate facility you are planning to use also has a non-climate controlled portion of their facility that may cost less.
These are just a few ideas to consider when trying to save money. As you know, every exhibition and every logistical situation is different. There is usually a good reason for being the cheapest guy on the block. Sometimes choosing a service provider with a better understanding of how to maximize the value you receive for your investment is the best way to deal with a over-stressed budget.
I know…this all seems like it is self serving considering that I am in the exhibition transportation business. The real issue is providing a valuable, safe, quality service that can come in under budget. The pros in this business can help you do this without causing you service nightmares. The guy that jumps at lowering his price to get your business needs to be considered carefully.
Coleman
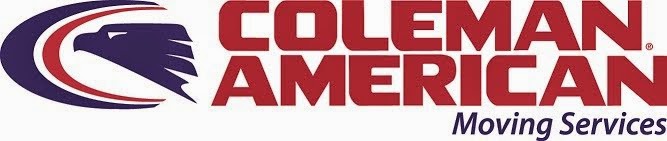
Friday, November 13, 2009
Tuesday, June 16, 2009
ITS NOT EASY BEING GREEN!
How we impact the environment is a concern in both our personal and professional lives. I spend lots of time talking either to people working in the transportation industry or those who need to use its services and, the reality is, the transportation industry uses a great deal of natural resources.
From the fuel required to transport each shipment to the paper and cardboard needed to pack the items we ship, the industry uses many consumables that have an environmental impact. However, we are actively implementing initiatives to minimize that impact.
Recycling: Safe transportation methods require the use of wood, paper and cardboard. We do everything we can to reduce, reuse and recycle. Our drivers and crews bring as much of the shipment packaging as possible back to the facility for recycling or reuse, as appropriate. Each of our facilities makes used cartons available to civic and cultural organizations that may have a need.
Brand New Packing…Again: We work closely with our vendors to ensure we get the best recycled materials available without sacrificing cleanliness or structural integrity. Reusable packing containers – like plastic bins and sturdy plastic speed bins are a few of the innovative materials that are commonplace on our projects.
We also have a number of environmentally focused initiatives in place on our trucks and trailers.
Generators: It was once commonplace to leave diesel engines idling for heat and electricity during stops. Now there are generator systems available to provide the on-board electricity needs and to warm engines for easier, more efficient starts.
Clean Machines: Closely monitoring maintenance schedules for our vans ensures that all our rolling equipment is operating at peak efficiency. Monitoring software alerts us to when equipment should have the oil changed, be lubricated, and even washed. We continually rotate out old, inefficient trailers and invest in modern, lightweight rolling stock to ensure that our fleet is operating at peak efficiency.
Tire Inflation: One way to minimize emissions, maximize fuel economy and tire wear is to utilize the P.S.I. Tire Inflation System. The U.S. Environmental Protection Agency recognizes this system effectiveness and recommends it as an industry standard.
EZPass & Prepass: The same EZPass transponders you use for toll roads, tunnels and bridges save drivers time and energy by eliminating fuel consuming idling and acceleration at toll stops.
Prepass transponders help drivers roll past weigh stations by sending all the appropriate information digitally to the station. If there are no weight or safety issues the driver gets a green light to continue on their journey without the fuel-consuming stop.
We’ve also looked to how we handle business within our facilities.
Paperwork: Documents don’t have to be documents. Many offices used to be consumed by massive filing cabinets filled with years- worth of documentation. No longer…we now create digital files of all the federal and state required documentation. We have eliminated literally tons of paperwork and made accessing information a quick mouse click away. Additionally, we recycle paper, printer cartridges and other office materials.
Office Equipment: Energy Star electronics save companies thousands in energy costs and represent a tangible example of wise energy management. We always look for the Energy Star Qualified label when purchasing equipment.
From the fuel required to transport each shipment to the paper and cardboard needed to pack the items we ship, the industry uses many consumables that have an environmental impact. However, we are actively implementing initiatives to minimize that impact.
Recycling: Safe transportation methods require the use of wood, paper and cardboard. We do everything we can to reduce, reuse and recycle. Our drivers and crews bring as much of the shipment packaging as possible back to the facility for recycling or reuse, as appropriate. Each of our facilities makes used cartons available to civic and cultural organizations that may have a need.
Brand New Packing…Again: We work closely with our vendors to ensure we get the best recycled materials available without sacrificing cleanliness or structural integrity. Reusable packing containers – like plastic bins and sturdy plastic speed bins are a few of the innovative materials that are commonplace on our projects.
We also have a number of environmentally focused initiatives in place on our trucks and trailers.
Generators: It was once commonplace to leave diesel engines idling for heat and electricity during stops. Now there are generator systems available to provide the on-board electricity needs and to warm engines for easier, more efficient starts.
Clean Machines: Closely monitoring maintenance schedules for our vans ensures that all our rolling equipment is operating at peak efficiency. Monitoring software alerts us to when equipment should have the oil changed, be lubricated, and even washed. We continually rotate out old, inefficient trailers and invest in modern, lightweight rolling stock to ensure that our fleet is operating at peak efficiency.
Tire Inflation: One way to minimize emissions, maximize fuel economy and tire wear is to utilize the P.S.I. Tire Inflation System. The U.S. Environmental Protection Agency recognizes this system effectiveness and recommends it as an industry standard.
EZPass & Prepass: The same EZPass transponders you use for toll roads, tunnels and bridges save drivers time and energy by eliminating fuel consuming idling and acceleration at toll stops.
Prepass transponders help drivers roll past weigh stations by sending all the appropriate information digitally to the station. If there are no weight or safety issues the driver gets a green light to continue on their journey without the fuel-consuming stop.
We’ve also looked to how we handle business within our facilities.
Paperwork: Documents don’t have to be documents. Many offices used to be consumed by massive filing cabinets filled with years- worth of documentation. No longer…we now create digital files of all the federal and state required documentation. We have eliminated literally tons of paperwork and made accessing information a quick mouse click away. Additionally, we recycle paper, printer cartridges and other office materials.
Office Equipment: Energy Star electronics save companies thousands in energy costs and represent a tangible example of wise energy management. We always look for the Energy Star Qualified label when purchasing equipment.
You are a member of the club!
If you have to transport anything by truck, plane, ship, bus or any other method that uses a gas or diesel powered engine, you are in a very large club. Unfortunately this club has some growing problems. Many of us have tried to convince ourselves that the problems are not ours, or that given time, they will go away. Time has run out!
I do not have the room to cover every problem we are facing but we should consider the big two, fuel costs and driver retention.
We have talked about the fuel surcharge in the past. We discussed how it is set and why it changes. By now, most of us understand the reasons for the surcharges and most importantly that we are all having to deal with the pain of these costs. Seventy percent of U.S. freight travels by truck and both the service provider and the consumer are getting hit by the sharp rise in the cost of crude oil. I’ve been told that 70% percent of the cost of diesel fuel comes from the cost of crude oil. The weakened dollar does not help with the cost of crude on the world market. Our economy may be slow, but countries like China have growing economies and this hurts the U.S. when it comes to our cost of crude.
Another major problem we are facing is the issue of driver retention. The entire industry is experiencing a shortage of qualified van operators. This demand has created a “churning” of drivers with many companies. This job-hopping creates a few problems. First, it creates added expenses due to recruitment and training of van operators, and it creates van availability issues for customers. The U.S. Dept. Of Transportation has also linked the job change rate to safety. Their research indicates that there is a relationship between the van operator change rate and crash involvement. The studies are not finished yet, but this information alone would indicate that greater scrutiny needs to be given during the hiring process. This is not just an issue of cost, but of public and cargo safety.
Links to current fuel cost information:
Diesel & Gasoline Comparison Prices (including a breakdown of derived costs)http://tonto.eia.doe.gov/oog/info/gdu/gasdiesel.asp
Diesel Prices Throughout the United Stateshttp://tonto.eia.doe.gov/oog/info/wohdp/diesel.asp
I do not have the room to cover every problem we are facing but we should consider the big two, fuel costs and driver retention.
We have talked about the fuel surcharge in the past. We discussed how it is set and why it changes. By now, most of us understand the reasons for the surcharges and most importantly that we are all having to deal with the pain of these costs. Seventy percent of U.S. freight travels by truck and both the service provider and the consumer are getting hit by the sharp rise in the cost of crude oil. I’ve been told that 70% percent of the cost of diesel fuel comes from the cost of crude oil. The weakened dollar does not help with the cost of crude on the world market. Our economy may be slow, but countries like China have growing economies and this hurts the U.S. when it comes to our cost of crude.
Another major problem we are facing is the issue of driver retention. The entire industry is experiencing a shortage of qualified van operators. This demand has created a “churning” of drivers with many companies. This job-hopping creates a few problems. First, it creates added expenses due to recruitment and training of van operators, and it creates van availability issues for customers. The U.S. Dept. Of Transportation has also linked the job change rate to safety. Their research indicates that there is a relationship between the van operator change rate and crash involvement. The studies are not finished yet, but this information alone would indicate that greater scrutiny needs to be given during the hiring process. This is not just an issue of cost, but of public and cargo safety.
Links to current fuel cost information:
Diesel & Gasoline Comparison Prices (including a breakdown of derived costs)http://tonto.eia.doe.gov/oog/info/gdu/gasdiesel.asp
Diesel Prices Throughout the United Stateshttp://tonto.eia.doe.gov/oog/info/wohdp/diesel.asp
Climate Van Equipment
When last you heard from me, I had just been asked about what equipment you should expect to be on a climate van. I continue to be asked this question and would like to answer it here.
First, a climate control van should be fully insulated and equipped with a cooling and heating unit. This unit will usually be diesel powered. This unit should have a high-capacity 50-to-1 compressor ratio that will allow it to operate in the most severe conditions. It should also have a panel in the driver’s line of sight that allows monitoring of the trailer climate status.
Hydraulic Lift Gates: Lift gates are not standard on all climate control vans, so you should make sure any of your quotes and orders specifically request a lift gate if needed. The Atlas Van Lines climate control vans are all equipment with lift gates with a capacity up to 5,500 lb. These gates also extend 8 to 12 inches above the floor of the trailer for access to higher docks.
Aluminum Cargo Beams and ¾ inch plywood sheets are useful as decking to add capacity to a trailer. These items can usually be stored beneath the floor to maximize available trailer space. Again, this equipment is not standard with every carrier so it should be specifically requested when needed.
Hydraulic Pallet Jacks: Almost every carrier has a pallet jack as standard equipment.
Logistic tracking and straps: This is standard equipment and is needed to secure any load.
Heavyweight pads: Pads are standard equipment and are used to protect delicate, un-crated objects during transit. Most full sized trailers carry about 12 dozen.
J- Bars: This is considered standard equipment. A six foot J-bar provides leverage that is useful for moving large crates.
Dollies: Four-wheel dollies and two-wheel heavy duty hand trucks are standard equipment for every carrier. These items provide easy mobility for crates, cartons and pad wrapped objects.
There are a number of additional items that may or may not be on a trailer. Some of these are large rubber bands, cartons and tape, riggers dollies, hydraulic rol-a-lifts, etc. These are not standard on every van but can be very helpful for handling some shipments. Always request these items from your carrier when needed.
First, a climate control van should be fully insulated and equipped with a cooling and heating unit. This unit will usually be diesel powered. This unit should have a high-capacity 50-to-1 compressor ratio that will allow it to operate in the most severe conditions. It should also have a panel in the driver’s line of sight that allows monitoring of the trailer climate status.
Hydraulic Lift Gates: Lift gates are not standard on all climate control vans, so you should make sure any of your quotes and orders specifically request a lift gate if needed. The Atlas Van Lines climate control vans are all equipment with lift gates with a capacity up to 5,500 lb. These gates also extend 8 to 12 inches above the floor of the trailer for access to higher docks.
Aluminum Cargo Beams and ¾ inch plywood sheets are useful as decking to add capacity to a trailer. These items can usually be stored beneath the floor to maximize available trailer space. Again, this equipment is not standard with every carrier so it should be specifically requested when needed.
Hydraulic Pallet Jacks: Almost every carrier has a pallet jack as standard equipment.
Logistic tracking and straps: This is standard equipment and is needed to secure any load.
Heavyweight pads: Pads are standard equipment and are used to protect delicate, un-crated objects during transit. Most full sized trailers carry about 12 dozen.
J- Bars: This is considered standard equipment. A six foot J-bar provides leverage that is useful for moving large crates.
Dollies: Four-wheel dollies and two-wheel heavy duty hand trucks are standard equipment for every carrier. These items provide easy mobility for crates, cartons and pad wrapped objects.
There are a number of additional items that may or may not be on a trailer. Some of these are large rubber bands, cartons and tape, riggers dollies, hydraulic rol-a-lifts, etc. These are not standard on every van but can be very helpful for handling some shipments. Always request these items from your carrier when needed.
Why is my invoice different?
Why is my invoice different from the quote I received a few weeks ago?
Howdy, I just hung up with Linda, a client that I have worked with for many years. She asked why the invoice she just received is different than the quote she received a few weeks ago. I thought that I did a pretty good job of informing our customers on pricing changes and the reasons they exist, but if Linda is asking this question…I better get more information out to everyone.
Here are some of the things Linda needs to know:
First of all we occasionally make a mistake, and due to human and/or computer error we send an incorrect invoice. This is an issue that not only creates problems for our customers, but creates major headaches for us as well. Not only have we failed our customer, but we have now created an accounting nightmare that takes more than a few man hours to correct.
By far, the largest factor in a changing quote is the fuel surcharge. The fuel surcharge is reviewed every month, by every carrier. With the ever changing cost of fuel, no carrier can ignore the effect on our pricing. At Atlas Van Lines we link our adjustments to the monthly Department of Energy reports. On the first Monday of every month, the DOE reports the average cost of fuel nationally. The fuel cost adjustment then becomes effective on the 15th of the month. (see our complete fuel surcharge matrix at www.atlasworldgroup.com/fuel). So…if you receive a quote today, the fuel surcharge could go up or down within a few days or weeks.
The second most likely reason for a change in your quote would be additional charges, not anticipated when you obtained your quote. If the van cannot reach the origin or destination site, there could be shuttle costs. A need for us to provide extra labor, deliver at overtime hours, make extra stops, or divert to a different delivery site can all create a change in the anticipated invoice. Providing as much information as possible is the best way to keep these costs down.
As service providers, carriers make every effort to keep clients updated on any changes to the price, but I must admit that it does not always get to the right people, therefore creating a surprise on invoice day.
Just as I finish writing this, I received an e-mail asking what equipment should be expected on a climate van…sounds like a good topic for next month.
Howdy, I just hung up with Linda, a client that I have worked with for many years. She asked why the invoice she just received is different than the quote she received a few weeks ago. I thought that I did a pretty good job of informing our customers on pricing changes and the reasons they exist, but if Linda is asking this question…I better get more information out to everyone.
Here are some of the things Linda needs to know:
First of all we occasionally make a mistake, and due to human and/or computer error we send an incorrect invoice. This is an issue that not only creates problems for our customers, but creates major headaches for us as well. Not only have we failed our customer, but we have now created an accounting nightmare that takes more than a few man hours to correct.
By far, the largest factor in a changing quote is the fuel surcharge. The fuel surcharge is reviewed every month, by every carrier. With the ever changing cost of fuel, no carrier can ignore the effect on our pricing. At Atlas Van Lines we link our adjustments to the monthly Department of Energy reports. On the first Monday of every month, the DOE reports the average cost of fuel nationally. The fuel cost adjustment then becomes effective on the 15th of the month. (see our complete fuel surcharge matrix at www.atlasworldgroup.com/fuel). So…if you receive a quote today, the fuel surcharge could go up or down within a few days or weeks.
The second most likely reason for a change in your quote would be additional charges, not anticipated when you obtained your quote. If the van cannot reach the origin or destination site, there could be shuttle costs. A need for us to provide extra labor, deliver at overtime hours, make extra stops, or divert to a different delivery site can all create a change in the anticipated invoice. Providing as much information as possible is the best way to keep these costs down.
As service providers, carriers make every effort to keep clients updated on any changes to the price, but I must admit that it does not always get to the right people, therefore creating a surprise on invoice day.
Just as I finish writing this, I received an e-mail asking what equipment should be expected on a climate van…sounds like a good topic for next month.
Subscribe to:
Posts (Atom)